What Are the Steps for Thermoforming Process for Medical Packaging?
Thermoforming is a plastic manufacturing process that involves heating a plastic sheet or roll to a pliable temperature, forming it into a specific shape using a mold, and then trimming the cooled part. The fundamental steps include:
- Sheet Heating: A plastic sheet (often from a roll) is heated in an oven to a precise temperature, making it flexible.
- Molding: The heated sheet is then draped over or drawn into a mold. Depending on the specific technique, vacuum pressure, positive air pressure, or mechanical force is applied to form the plastic against the mold’s contours.
- Cooling: The formed plastic is rapidly cooled to solidify its shape.
- Trimming: Excess material is trimmed away, and the finished custom medical tray or clamshell is ejected.
Modern thermoforming machines incorporate advanced controls for temperature, pressure, and dwell time, ensuring repeatability – a vital aspect for regulated medical applications.
What are Common Materials in Thermoforming Medical Packaging?
The selection of materials for thermoformed medical packaging is driven by stringent requirements for biocompatibility, chemical resistance, clarity, and compatibility with sterilization methods.
Note specific medical-grade plastics used in thermoforming, for sterile barrier systems:
- PETG (Polyethylene Terephthalate Glycol): One of the most common materials for PETG Medical packaging. It offers excellent clarity, toughness, chemical resistance, and is compatible with various sterilization methods. Its amorphous nature makes it easily thermoformable and it maintains its properties post-sterilization.
- Polycarbonate (PC): Known for its high impact strength, transparency, and heat resistance. It’s often used for durable medical device housings and trays where superior strength is needed.
- High Impact Polystyrene (HIPS): A cost-effective material, easily thermoformed, and can be used for general medical trays where high clarity or strength isn’t the primary requirement. It’s less common for sterile barrier systems due to its more opaque nature and lower chemical resistance compared to PETG. It is often used for multi-cavity medical shipping trays.
- Polypropylene (PP): Offers good chemical resistance, can withstand higher temperatures, and is often used for autoclavable applications.
- PVC (Polyvinyl Chloride): While historically used, its use is declining in some medical applications due to environmental concerns and plasticizer leaching. When used, it’s chosen for flexibility and clarity.
- APET (Amorphous Polyethylene Terephthalate): Similar to PETG but without the glycol modification, offering good clarity and barrier properties.
Are Environmentally Friendly Materials Available for Medical Thermoformed Packaging?
Bio-based plastic rolls are emerging as viable alternatives for thermoformed packaging trays for medical components. These materials offer a more environmentally friendly option. Bio-based plastic rolls comply with FDA standards for packaging, ensuring they meet the necessary safety and performance criteria for medical applications. Materials are compatible with common sealing processes, allowing manufacturers to reduce their environmental footprint. This information was shared by Good Natured Products. Link below for details. //goodnaturedproducts.com/pages/bioplastic-roll-stock-extruded-sheets
Other Environmental Considerations:
- Material Selection: PETG or RPET (recycled PET) are commonly recycled.
- Design for Recyclability: Designing trays to be easily separable from other packaging components (e.g., lidding) and avoiding multi-material laminates where possible can facilitate recycling.
- Design to Minimize Material: Function is key. A design which uses less material is generally less expensive and better for the environment.
What is the Key Design Criteria for Device Protection in Custom Medical Trays?
Custom medical trays are engineered to protect it from physical damage, particulate contamination, and provide optimal device presentation to end-users in a clinical setting.
Key design elements include:
- Custom Cavities: Precisely formed cavities cradle the medical device, preventing movement, abrasion, and damage during transit and storage. This often involves intricate geometries to match the device’s contours and can allow for clearance areas which don’t contact the medical device.
- Retention Features: Undercuts, snap features, or ribs can be integrated to securely hold the device in place, preventing dislodgement even under vibration or shock.
- Visibility: Clear materials like PETG are often chosen to allow visual inspection of the device without opening the package, aiding inventory management and pre-procedure checks.
- Aseptic Presentation: Designs facilitate easy, controlled removal of the device from the package in a sterile environment, minimizing the risk of contamination during presentation. This includes features like peelable lids and finger tabs.
- Stackability and Nestability: Trays are often designed to stack efficiently for shipping and storage when empty (nestable); and are stackable when packaging trays are full of medical components.
- Ribs and Reinforcements: Strategic placement of ribs or thicker sections can enhance structural rigidity without significantly increasing material usage.
What are the Advantages of Thermoforming Compared with other Manufacturing Processes for Medical Trays?
- Tooling Cost & Speed: Thermoforming has significantly lower tooling costs and shorter tooling lead times compared to injection molding. Since only one side of the mold defines the intricate features (the other side being formed by vacuum/pressure), tooling is simpler and quicker to fabricate.
- Part Size & Thickness: Thermoforming is ideal for producing large, thin-walled parts, and is cost effective for disposable shipping trays. Injection molding offers superior dimensional precision for high tolerance requirements.
- Material Flexibility: Thermoforming has a wide range of thermoplastic sheet materials available, including those specifically formulated for medical applications. This includes multi-layer barrier materials.
- Prototyping: The lower tooling cost and faster turnaround make thermoforming excellent for creating prototypes and testing concepts.
- Sterile Barrier Integrity: The primary function is maintained through robust seals and material selection.
- Physical Protection: Resistance to impact, vibration, compression, and abrasion during shipping, handling, and storage.
- Chemical Resistance: Ability to withstand exposure to cleaning agents, sterilants, and the packaged device’s own chemical properties without degradation.
- Temperature Stability: Maintaining structural and barrier integrity across a range of temperatures encountered during transit, storage, and sterilization.
- Puncture and Tear Resistance: Critical for maintaining the sterile field and preventing damage to the packaged device. This is particularly relevant for lidding materials like Tyvek.
- Visibility and Clarity: Essential for product identification, inspection, and proper presentation.
How are Trays and Clamshells Sealed?
- Heat Sealing: Tyvek offers a heat-activated adhesive layer on the lidding material (e.g., Tyvek, medical-grade paper, or film) is bonded to the flange of the thermoformed tray using controlled heat, pressure, and dwell time.
- Advantages: Creates a strong, consistent, and validated sterile barrier. Allows for easy peel-open functionality for aseptic presentation. Compatible with various lidding materials.
- Disadvantages: Requires precise control of temperature, pressure, and dwell time. Overheating can damage materials.
- RF (Radio Frequency) Welding: This process creates a strong, hermetic seal by using high-frequency electromagnetic energy to heat and melt the plastic at the molecular level, followed by pressure application.
- Advantages: Creates extremely strong, clean, and consistent seals without external heat. Ideal for thick-gauge materials or applications requiring exceptional seal integrity.
- Disadvantages: Limited to specific thermoplastic materials (e.g., PVC, polyurethane) that respond to RF energy. Higher equipment cost.
What are some Key Medical Applications Which Use Thermoforming?
- Surgical Instruments: Custom medical trays are designed to hold individual instruments or full surgical kits, ensuring they remain sterile and organized.
- Diagnostic Kits: Trays for organizing vials, reagents, and other components of diagnostic test kits.
- Pharmaceutical Blister Packs: Common for pills and small doses, offering tamper evidence and controlled dispensing.
- Catheters and Tubing: Trays designed with channels and retainers to prevent kinking or damage to flexible medical tubing.
- Work-in-Process (WIP) Trays: Used internally within manufacturing facilities to protect components between manufacturing stages; and for shipping machined medical components to the end customer. Some examples of some off-the-shelf medical trays are shown here: //ecpplastictrays.com/product-category/shipping-trays/medical-trays/
What Are the Most Common Sterilization Methods?
- Ethylene Oxide (EtO) Sterilization: Many common thermoform plastics (e.g., PETG, HIPS) are compatible with EtO.
- Gamma Radiation Sterilization: PETG and some grades of PP and PC are compatible. However, some materials can become brittle or discolored (yellowing) with high doses. PETG is generally robust.
- E-beam (Electron Beam) Sterilization: Similar to gamma in terms of material compatibility. It offers faster processing times and less material degradation in some cases compared to gamma, as it involves less penetrating radiation.
- Steam (Autoclave) Sterilization: Requires materials with high heat resistance, such as polypropylene (PP) or some polycarbonates, as it involves high temperatures and moisture. Not all thermoform plastics are suitable. Material degradation can include warping or melting if the material’s heat deflection temperature is exceeded.
What are the Thermoforming Processes used in the Manufacture of OEM Medical Equipment?
- Vacuum Forming: The heated plastic sheet is pulled into or over a mold by vacuum pressure.
- Advantages: Cost-effective, good for basic shapes, fast cycling. Effective for interior utility components like trays, or bins, and clear parts.
- Disadvantages: Less precise control over wall thickness distribution, limited detail compared to pressure forming.
Pressure Forming: Similar to vacuum forming but uses positive air pressure on the non-mold side in addition to vacuum. Images of pressure formed healthcare components can be found at //thermoform.com/industries-healthcare/.
- Advantages: Pressure forming provides highly detailed surfaces, molded-in features like undercuts, and close tolerances. These benefits deliver fit and function comparable to injection molding with significantly reduced project costs. Pressure forming uses custom-color thermoplastic materials optimized for medical applications like enclosures and cover panels for medical devices.
- Disadvantages: Higher tooling costs and slightly longer cycle times than vacuum forming.
Twin-Sheet Thermoforming: Two plastic sheets are simultaneously heated and formed, then fused together to create hollow or double-walled parts. This process is more common with Thermformed OEM Component parts.
- Advantages: Creates strong, rigid, hollow structures, often used for instrument cases or complex device housings. Eliminates secondary assembly steps.
- Disadvantages: More complex tooling and process control.
What Are Cleanroom Options with Thermformed Packaging Manufacturing?
- Cleanroom Thermoforming: Production of primary medical packaging, especially custom medical trays, often takes place in an ISO Cleanroom environment (e.g., ISO Class 8) to control particulate contamination. These controlled environments regulate airborne particles, temperature, humidity, and pressure. Read more about medical tray cleanroom levels: //ecpplastictrays.com/ideas/medical_trays_cleanroom_levels/
- Contamination Prevention: Additional strategies regarding cleanliness include material handling protocols, employee gowning, air filtration, and regular environmental monitoring.
- Cleanroom Cleaning of Thermoformed Parts. Parts are processed through a state of the art particulate trap system in a ISO Class 7 Cleanroom, effectively removing microscopic particles and debris.
GUIDE SUMMARY
We would like to thank Profile Plastics for sharing some of the information in this article. Profile Plastics is active in The Society of Plastics Engineers Thermoforming Division; and specializes in thermoformed component parts for medical equipment. Details can be viewed at //thermoform.com/.
Thermoforming is used for Healthcare OEM Panels and Equipment and for Medical Packaging including plastic trays. By using best practices for the design and materials, the project cost and lead times can be shortened, while optimizing function and reducing environmental impact. “Packaging Engineer’s Guide to Medical Thermoformed Packaging” was written by Chris Spiegel: President of Engineered Components & Packaging.
View our Plastic Medical Trays & Packaging Page HERE.
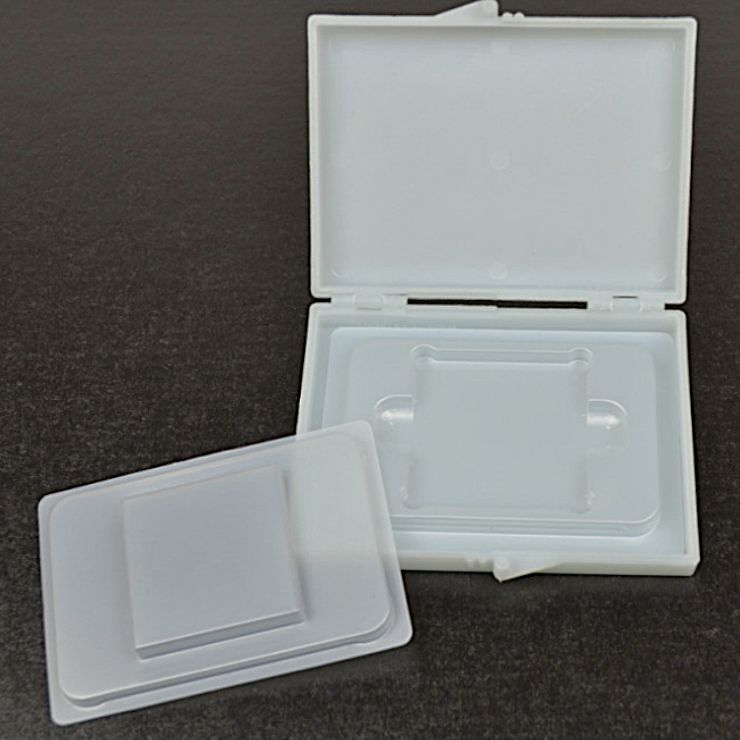
Chris Spiegel – cespiegel@ecpplastictrays.com