How do you package small fragile parts in boxes, & bins?
There are several methods to segregate small parts. The most common methods include dividers or insert trays. Insert trays are discussed elsewhere. Below we review dividers noting the different types, the benefits, and highlighting some photos of each style. THESE ITEMS ARE CUSTOM. A ECP PACKAGING PROJECT MANGER WILL WORK WITH YOU FROM QUOTE TO PRODUCTION. CONTACT US TO REVIEW.
6 SECTIONS BELOW:
(1) Plastic Dividers For Bins | (2) Plastic Corrugated Dividers | (3) Foam Dividers
(4) Coated Dividers | (5) Fluted Dividers for Cylindrical Parts | (6) ESD Dividers
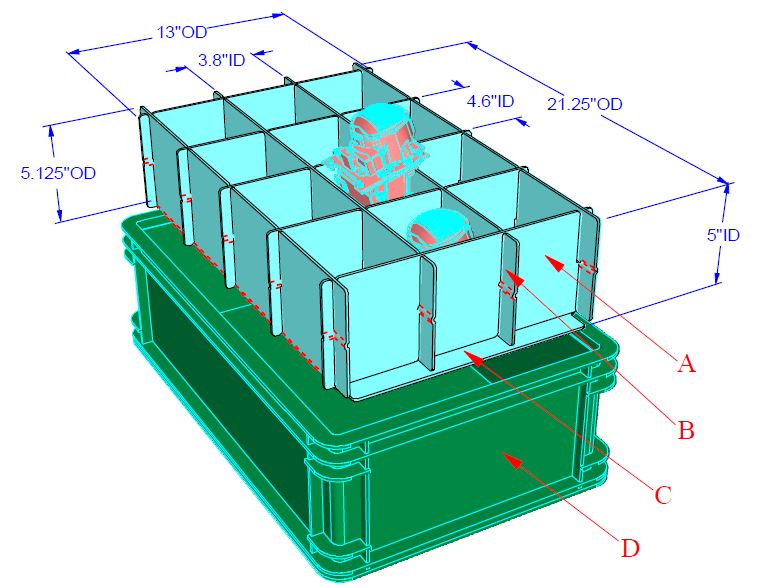
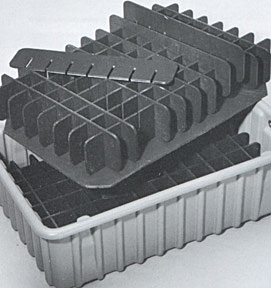
Plastic Dividers for Bins
1) Plastic dividers are made to fit the bin.
2) Different cavity spacing can be created by using more or fewer dividers. The smallest cavity spacing is 1.25″ X 1.25″ with most bins. Sizes increase in increments of 1.25″. This allows for small cavities or long narrow cavities in the same bin.
3) Plastic Bins and Plastic Dividers are very durable with a long project life. Bin spacing can be changed if the project changes. Both products can be reused.
4) Made from 1/8″ heavy duty plastic.
5) Bin dividers can be used for boxes and other containers but work best with grooved plastic divider bins. See Bin Size Chart HERE.
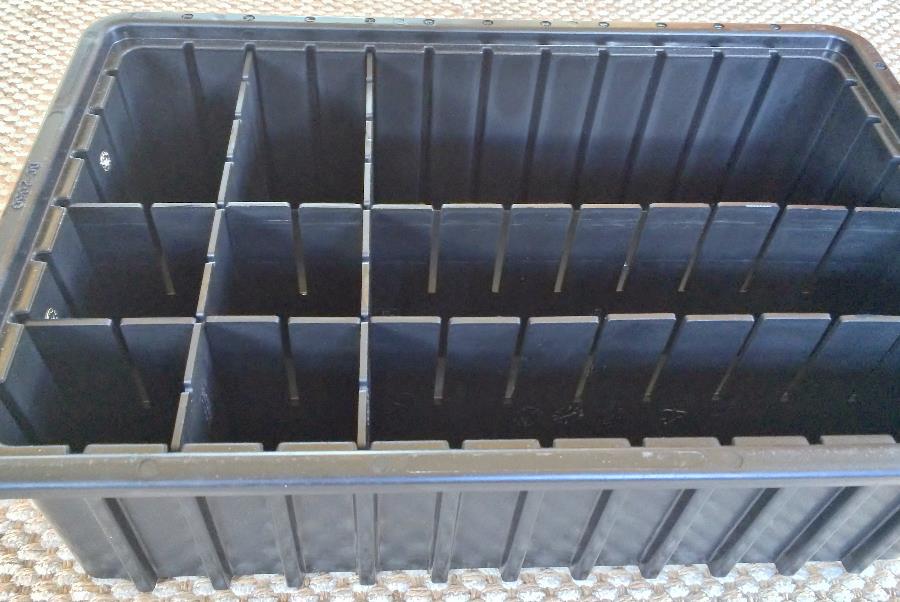
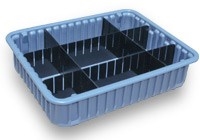
Plastic Corrugated Dividers for Boxes, Bins, Containers
1) Custom and can be made in any size for any compartment size.
2) Little or no tooling cost.
3) Plastic corrugated when designed well creates a strong long lasting product.
4) Good option for low to mid volume applications based on low tooling cost and flexibility in customizing.
5) Divider can break down flat.
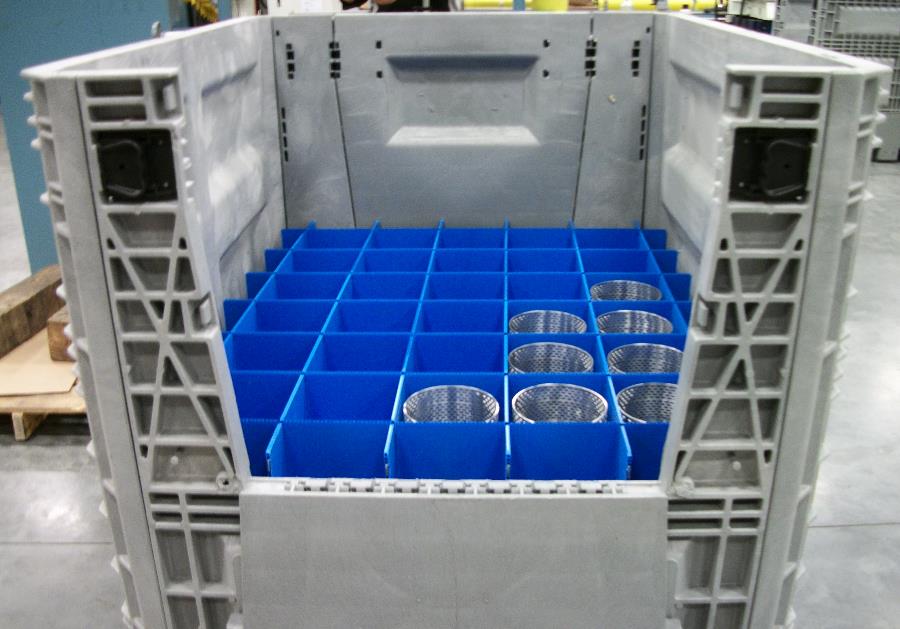
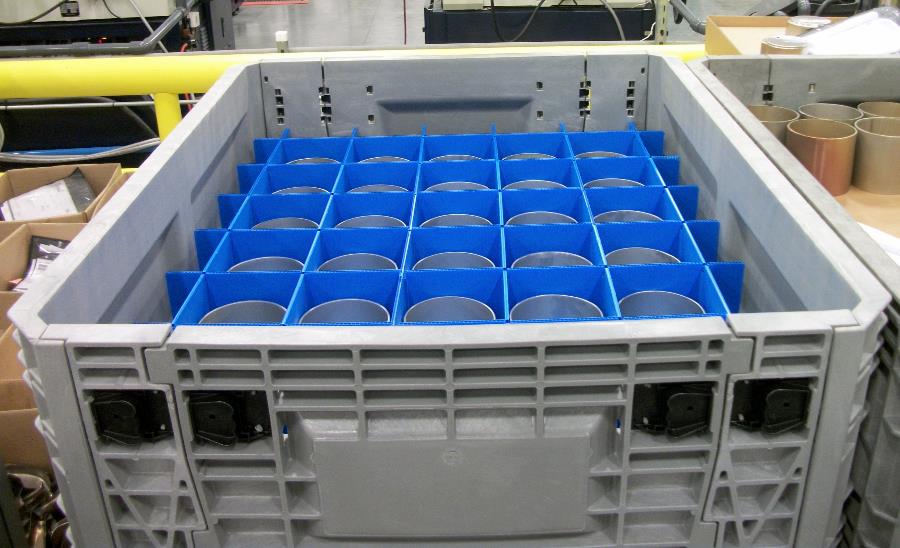
Foam Dividers for Plastic Bins and Containers
1) Excellent strength and cushioning for product. It is a good choice with heavy products which can not touch each other in shipping. It can be used as a kit with different items or for multiple compartments of the same item.
2) The foam inserts can be made any thickness depending on application. And can be made to any compartment size.
3) Materials are available with good structure, which are rated for Class A surfaces, or are ESD. Different densities can be used depending on application.
4) Little set up or tool cost. Most projects have a $ 95. NRE.
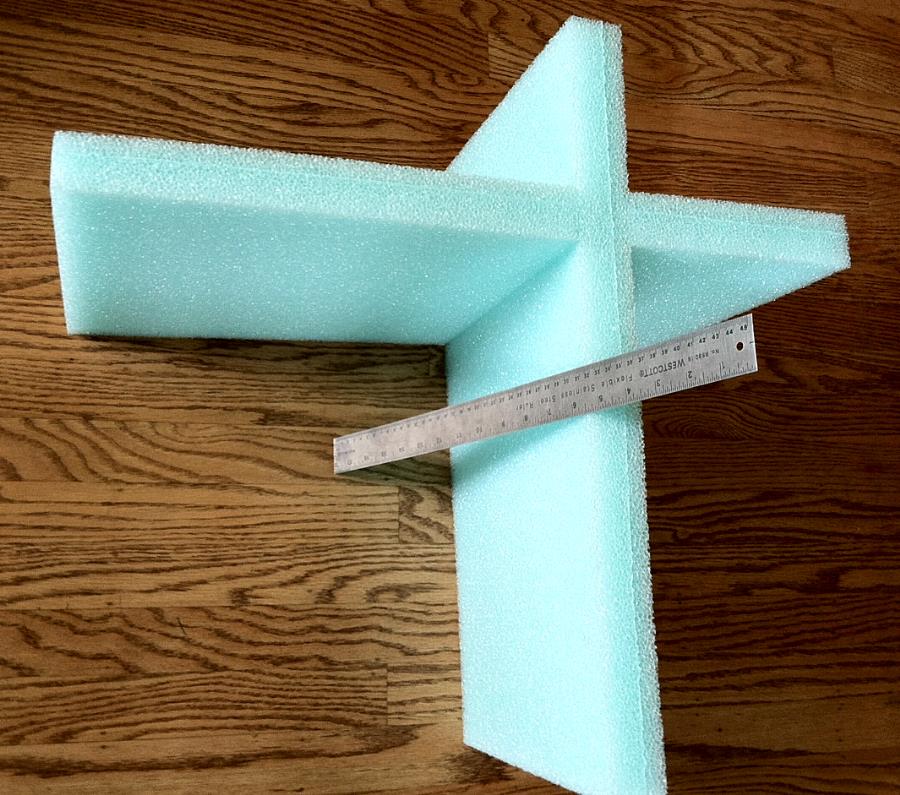
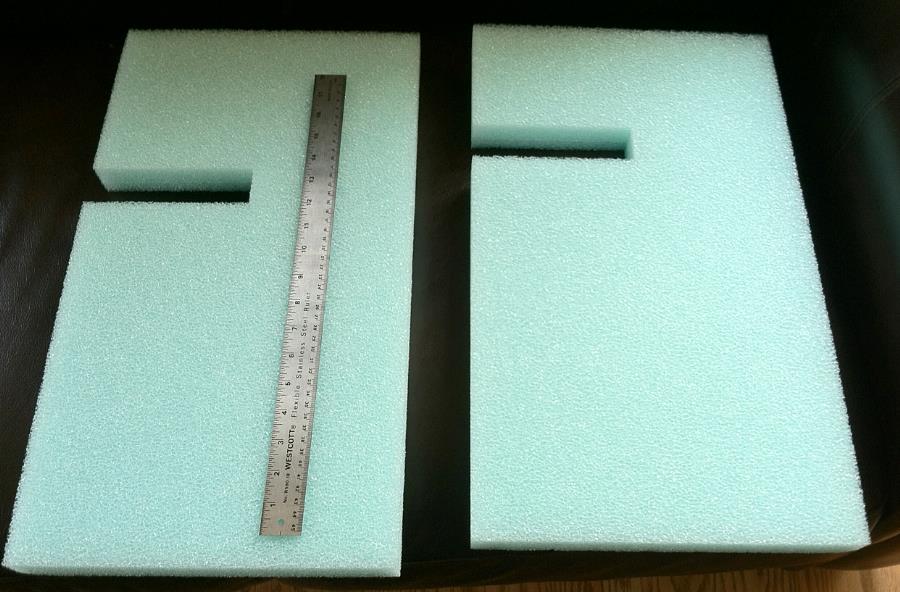
Coated Dividers for Part Shipments
The corrugated material is covered with a coating to minimize any corrugated dust or contaminants. These are just slightly more expensive than standard paperboard or chipboard style dividers. Advantages of the chipboard coating include:
1) Low cost allows to be a disposable packaging item. This is typically used for machined parts which are sensitive to dust or particulate.
2) Cleaner than standard chipboard with less debris. The coating eliminates much of the corrugated contamination.
3) Allows for tall narrow cavities on items like bottles or cylindrical parts. Where plastic thermoformed insert trays have limitations for depth, divider sets can be as tall as needed.
4) Chipboard sets fold down and ship flat. These are easily opened and completely assembled for insertion into box with no extra labor needed.
- Products shown here are for industrial shipping applications. For retail storage dividers, there are many sources available including Walmart.
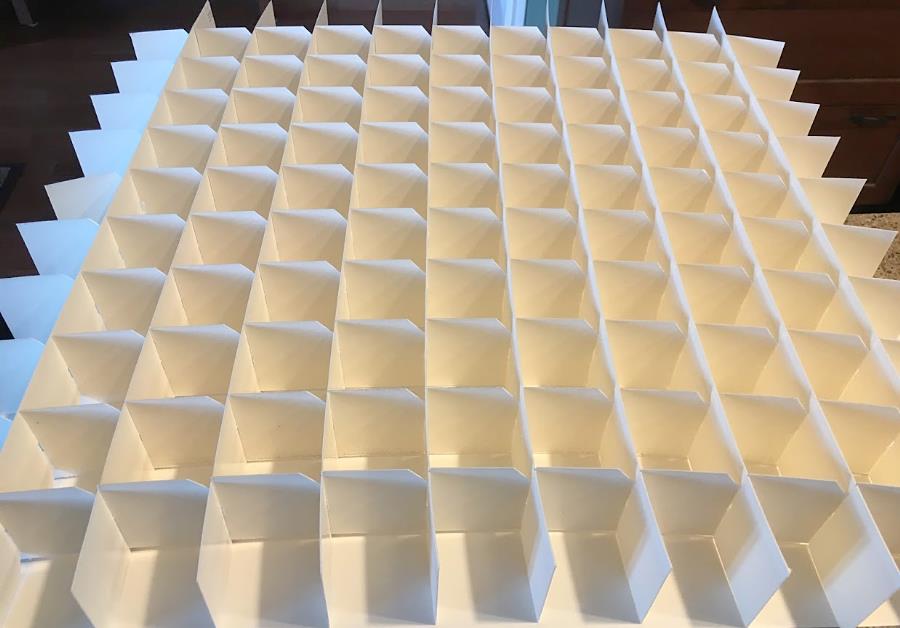
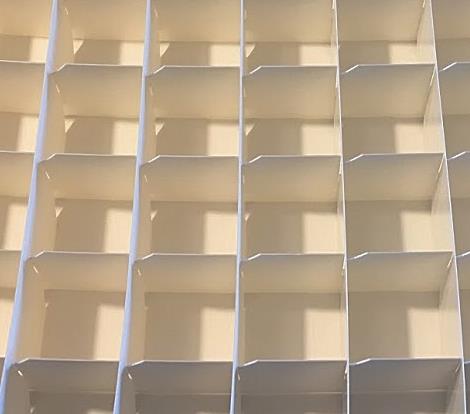
Fluted Trays for Bottles and Cylindrical Parts
1) No tooling cost if diameter falls within one of the 50 or so stocked tools.
2) Can be assembled or fit to a box or can be a stand alone tray. There are multiple box configurations.
3) Low cost method of packaging cylindrical parts, tubes, bottles, and machined parts from high speed machining centers.
4) Short lead times for custom applications 1-2 weeks ARO.
5) Samples available.
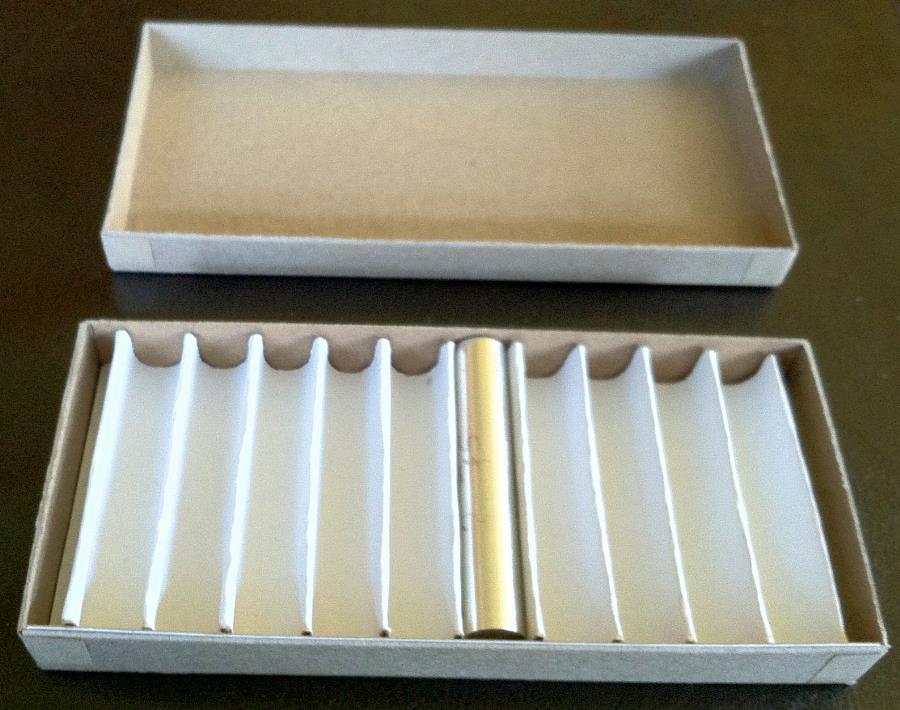
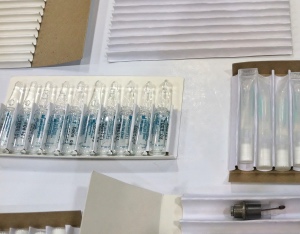
Corrugated ESD Dividers for Electronic Components
1) Significantly minimizes labor of using ESD bags while maintaining part protection. This is an advantage to the component manufacturer who has to package as well as the customer who has to remove the parts.
2) Different styles and cost levels of the ESD products are available depending on the application. The shipping style can be more cost effective, flatten when shipped, and open as a assembled unit.
3) This is a low cost option for larger or long parts which don’t fit into stock trays or standard packaging.
4) Tool cost is low for a custom sized box and divider set made to fit your current ESD bin.
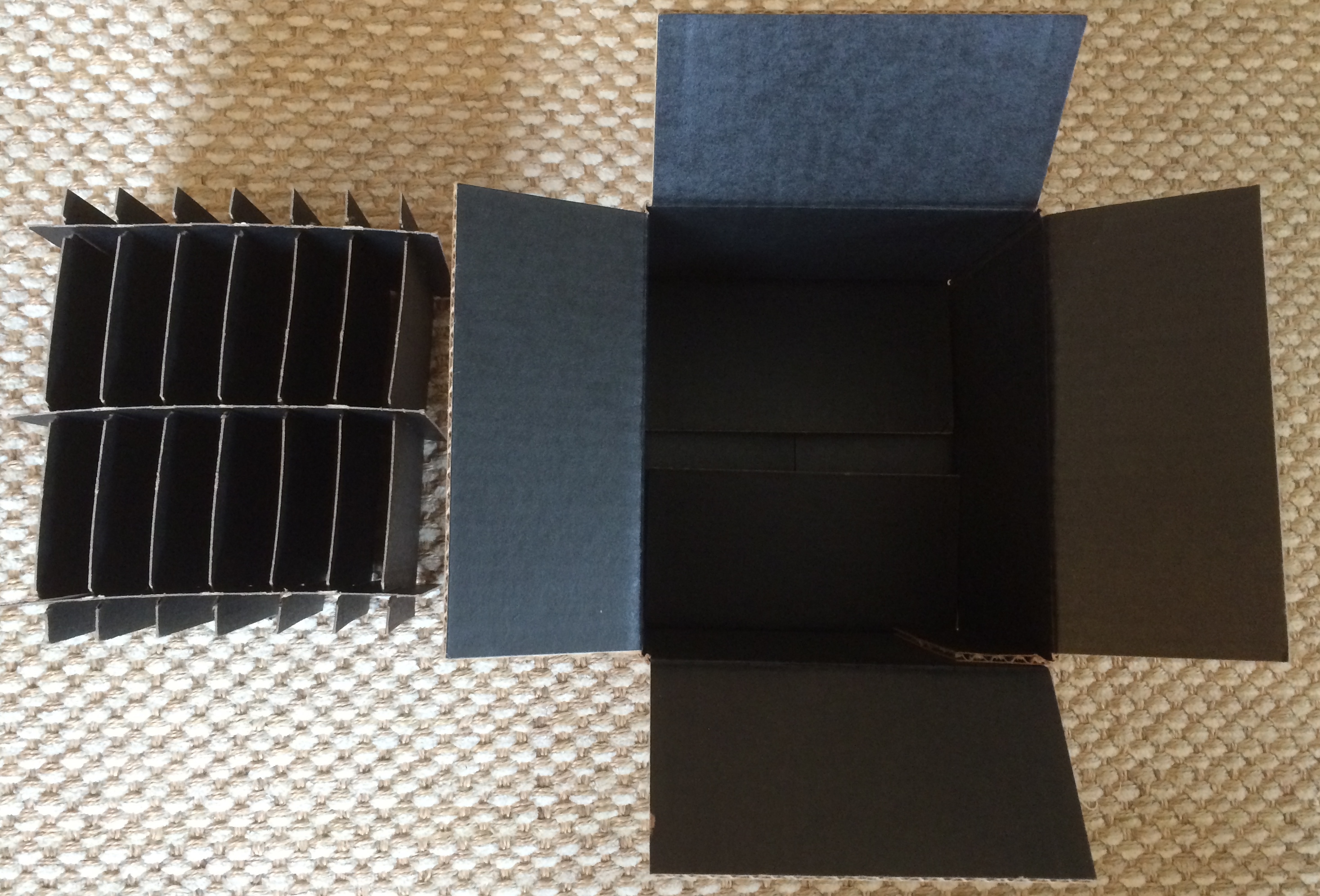
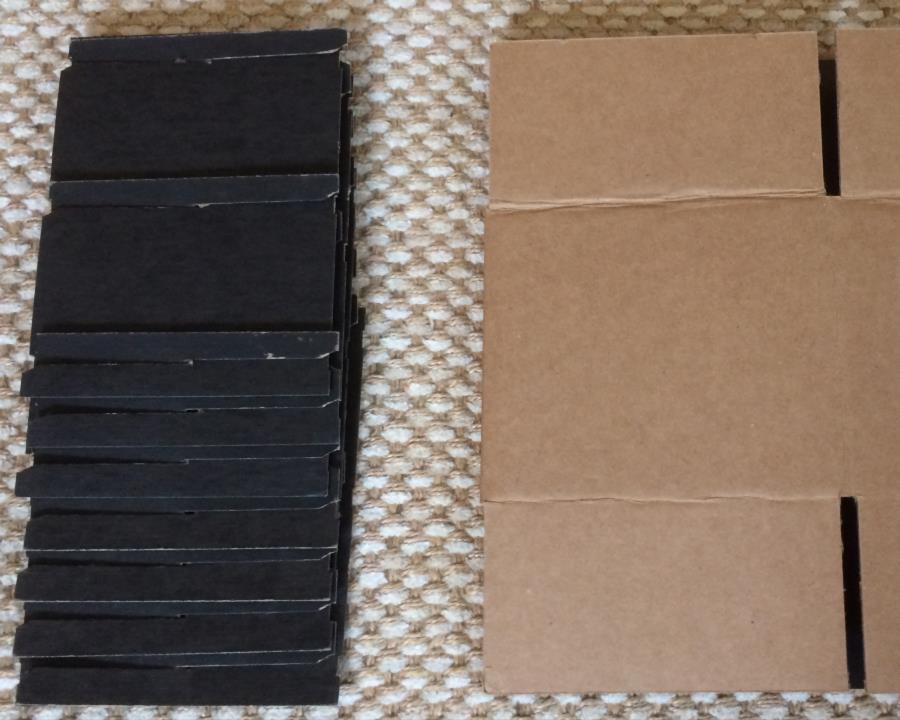