Custom Automation Trays for Robotics
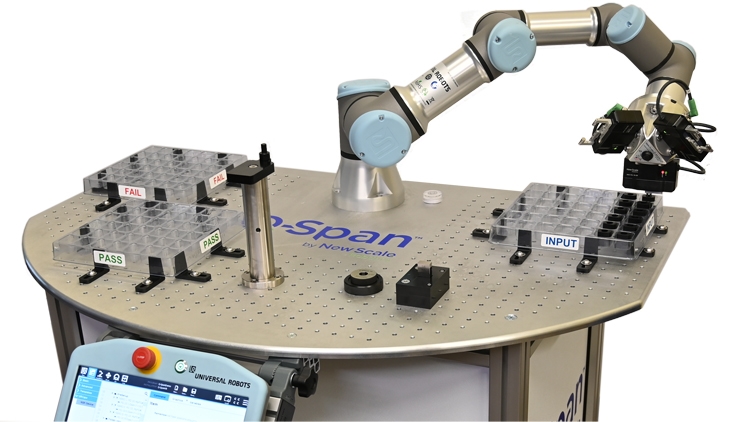
Example above shows the Q-Span Automated Small Part Measurement System with UR collaborative robot; used for part inspection. This unit automatically picks parts from the “input” tray, measures multiple dimensions on each, then makes decisions where to place the parts – for example, into the “pass” or “fail” tray. The example shown is a full workstation solution with custom trays designed for the user’s part.
Tray Design Considerations for Robotic Arm Applications
Locating the Tray: The robotic system must be able locate and access the components and locate the trays and components in the tray. This can be accomplished in different ways.
Mechanical features can be added to the tray so it can be used along with a fixture(in a set location), or with a backstop to orient the tray for the robotic arm. Parts can then be oriented and arranged in a pre-designed matrix using cavities for locations and for part orientation. Cavities can be standard geometric shapes or can be shaped to fit the part. When shaped to fit the part, fragile areas of the part can be in a clearance section of the cavity preventing it from contact with the tray. NOTE: mold features and not trim features should be used.
Visual systems can be used for locating the tray for the robotic system. With a visual system, a feature or symbol can be molded into the tray for orienting the optics. Or an area or pattern can be machined out of the tray to orient the optics. Light beams can confirm tray orientation viewing through multiple trays at once. This usually requires a hole or feature in the tray used as a locator. Orientation features like a chamfer on a corner or other tray feature can be used to error proof location and stack orientation.
Part Gripping or Placement: The part must be placed in or removed from the tray. Common methods robotic part placement include suction cups, grippers, or gravity. Clearance sections can be added to allow space for the gripper; or cavity shape can be used to orient the part in the needed position in the automation tray. The tray manufacturer often works directly with the automation company to develop the tray in conjunction with the picker heads, and pick and place equipment to ensure proper function.
Stacking: Stack features can be used to stack trays. The least expensive way which does not require undercuts is 180 rotational stacking. The tray above will stack on the tray below with no load on parts when rotated 180 degrees. With 180 stacking trays will nest when empty taking up minimal space. Undercuts can also be used with stacking. With this method no rotation is needed but trays will not nest.
Material: ESD or standard materials can be used in multiple gauges. Considerations include gauge of material for tray, flatness of material when formed, washability, durability, and cost. With some applications thick material is used for a fixture tray along with thinner material for the automation insert tray. Different inserts are then used with the same heavy duty tray and thin gauge tray is then used for shipping.
Design Tray Early: There are many other considerations. It is important when designing a system to get the tray supplier involved early in the design. This will help keep costs down and avoid unexpected delays. For reference and other considerations see the Custom Tray Design Guide.
Robotic Arm Automation Background
Automation has advanced to a point where robotics can now look very different depending on the application. There are differences in speed. High speed automation is often used for applications such as (1) pick and place, (2) pick and pack, (3) packaging and palletizing. A robot or robotic arm can move at a speed almost tough to follow with the human eye. Many of these applications require guarding due to the speed.
Low speed applications can include manufacturing bench jobs, and inspection of components allowing equipment to automatically measure small parts. With low speed applications a robotic arm moves approximately at the same speed as a human arm would in the same application. These robotic arms generally do not require special guarding.
Advantages of robotic arms are many. With repetitive jobs, robotic automation:
- reduces repetitive stress injuries in operators
- avoids operator boredom
- maintains consistent pace
- maintains accuracy in the process.
- uses less space than an operator would require for the same operation.
With high speed automation, robotic arm automation:
- increases throughput for the operation
- reduces part cost making product more competitive in market
- reduces operator injuries
- reduces downtime
- allows for the ability to work multiple shifts or lights out.
Many applications, regardless of speed, use automation tray packaging or fixture trays for handling parts during the process.
More information on this topic is available by contacting Chris Spiegel with Engineered Components & Packaging, LLC. See Contact Us.