Custom Thermoformed Tray Design Guide
Our INTERACTIVE DESIGN GUIDE below highlights Custom Tray Applications, Design Features, Material Options & Advantages of Custom Trays & Inserts. This custom trays design guide was created to assist packaging engineers, and others, tasked with custom thermoform tray design and sourcing. Click + to open additional pages.
Tray Design Features | Best Practices
Common Design Features reduce packaging cost, and reduce labor time.
STACKING
Stacking features can be designed to allow tray stacking with no load/ no contact to parts. This is different than nesting (see video above). Stacking features and nesting features can be designed into the same tray for shipment when trays empty; and for part protection. Lids are not required with proper stack features reducing packaging cost.
EASY PART HANDLING WITH FINGER GROOVES
Trays can be designed with finger clearance or tweezer clearance for easy placement and removal of parts. These form features or grooves can be molded in at locations where part contact is preferred.
EASY COUNTING WITH NUMBERED CAVITIES
Cavities can be in even numbers like 50 or 100 to facilitate counting. Numbers can be molded in for each cavity for inspection or other applications. Embossing of numbers adds no cost to piece price and slight cost to tooling.
KITTING TRAYS FOR STAGING PARTS
Kitting trays can be made for assembly operations. This can be a tray with a specific number of cavities or with cavities sized to fit part. The tray color can contrast the parts allowing easy identification if missing a part needed for a assembly. These kits can be prepared for assembly stations in lean manufacturing environments and help insure there ar no items left out when assembled. An example is a medical device tray.
LIDS OFFER EXTRA PROTECTION AND FEATURES
CLICK photo for Video
Lids can be designed to fit a custom or stock tray. Lid can be clear for visibility or can include form features which fit into cavities and prevent movement and cavity jumping in very small part packaging. Tray can be opaque (black or white) with a clear look for part visibility. Embossing of logo or website also possible on lid.
AUTOMATION
Locating features can be added to assist with optical or mechanical robotic part placement. Form features in tray are the best places to locate for robotic cavity placement vs. the perimeter cut. Accuracy and consistency is controlled by the tool with form features.
NESTING
Nesting, when built into the tray design, keeps space requirements low for transport of empty trays. Nesting is different then stacking. Nesting is when a tray fits inside another tray when empty; like plastic cups. Stacking is when features are built in tray to stack at a specific dimensional height where no weight is on the packaged part.
SNAPS
Friction fit, indentations and undercuts can be used to hold part or to fasten cover or tray lid. Button snaps, perimeter snaps or slight undercut areas are the most common methods.
ENGRAVING
Company name, company website, and part numbers can be molded into tray with no additional part cost. Numbered cavities can be molded on tray. Special notes can be molded into tray. Notes such as “Return to …..”.
DE-NESTING LUGS
Some materials stick when nested. This design feature allows for easier separation of trays; and handling of trays by operators.
LIVING HINGE
This is a feature in plastic clamshells which attaches the cover to the tray. Often snap features are included with clam-shell packaging or clam-shell can be heat sealed. This is usually used with retail packaging. There is added design cost compared to a unhinged tray and cover, or a stacking tray.
HAND ACCESS for Removal From Box or Bin
This is a feature allows for the tray to be removed reaching into a box or bin. See image for explanation.
PRINTING
Printing and contour printing on packaging for higher volume applications. This process creates a Vivid 3D image directly on the formed thin gauge plastic. Main area for this is retail and food. Not typically used for industrial packaging.
Material Considerations For Custom Trays
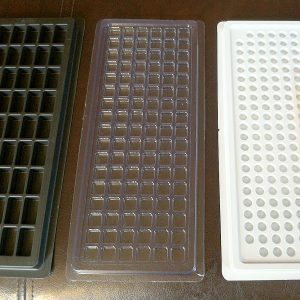
Material Selection is a key decision when specifying a tray. Key variables when choosing a material include, ESD requirements, impact resistance, budgetary constraints, operating temperature, chemical resistance, cleanliness with regard to applied coatings, clarity (clear vs. opaque), color, and sealing technique if applicable. Common materials are described below in this section.
Material Considerations
- Cost
- Chemical Resistance
- ESD Requirements
- UV Resistance
- Coatings applied to materials for ESD protection or de-nesting. (medical)
- Wash-ability
- Durability
- Heat Deflection
Custom Trays Material Thickness
- Plastic Material Thickness (Notes intended as a guide dependent on depth of tray and many other factors)
1) .015″ to .030″ starting thickness is common for disposable shipping trays for small parts.
2) .030” to .060” starting thickness for use for a number of cycles but not long term.
3) .060″ to .375” starting thickness for long term reusable trays.
- Molded Pulp Material Thickness (2 options)
1) .⅛” standard gauge molded pulp. This is typically used for shipping and lighter items.
2) .250” heavy gauge molded pulp is very durable used for skids, trays, and heavier parts.
Common Materials For Shipping | Reusable Trays (Non ESD)
- High Impact Polystyrene (HIPS Tray Material used for shipping and reusable trays)
Thin and heavy gauge options. Low cost material for shipping or reusable trays comparable in price to PVC Clear. Styrene is readily available in black and white. Styrene is more rigid than PVC with the possibility of cracking on corners with reuse. ESD options below.
- HDPE Tray Material (used for shipping trays in special applications and for automotive trays)
Thin and Heavy Gauge options. Material is softer, has good impact strength, and excellent chemical resistance. It is also good for low temperature applications.Disadvantages include tendency to warp which make it difficult to use for trays that need to be flat for automation applications. Also very difficult to bond to HDPE.
- PVC (used primarily for small parts shipping trays)
Advantages: 1. Low cost 2. Durable (longer lasting than styrene in comparable thickness) 3. Clear 4. Good chemical resistance(see chart) 5. Available in ESD with a anti-static non silicone coating (see ESD Options)
Disadvantages: 1. Generally has a denesting agent allowing trays to be separated when nested. This is an applied coating which often includes silicone 2. Due to silicone coating, may not be good option for medical applications depending on sensitivity of application
- PETG Material (used for shipping trays and reusable trays)
Thin and Thick gauge options. PETG is a Clear Polyester. It has excellent strength for use in packaging trays and is a low outgasing material. Common applications include medical and optics. It may have a de-nesting agent similar to PVC which can be silicone. Also available with an Anti-Static Coating, Inherently Anti-Static, or Un-Coated.
- Polypropylene (often used in medical trays for shipping or storage)
Polypropylene has unique chemical resistance properties, and resists heat allowing it to go through some sterilization processes like autoclave. Often used in medical applications. PP is a softer material and also can be difficult to maintain flatness.
- Polycarbonate (used in high heat applications and for lab trays)
Polycarbonate is more expensive by a factor of 5 compared to the low cost packaging items. Key advantage to using polycarbonate is the higher heat deflection temperature (see below). Recommend testing in specific application.
Heat Deflection Temperature: 270 degrees Fahrenheit
Continuous Use Temperature (= 24/7): 180 degrees Fahrenheit
Intermittent Use Temperature: 257 degrees Fahrenheit
- ABS Material (primarily for reusable trays)
Thin and heavy gauge options. Material has good impact resistance. It is often used with drip trays or automation trays as material stays flat. Most common color is black. Fairly low price but more expensive than Styrene, PVC, and PETG.
- Foam Material (rigid)
Foam trays are available in Polyethylene and Polyurethane in multiple densities and in Anti Static and Conductive materials. Polyethylene is a stiffer material better if parts have weight. Polyurethane is a softer material potentially better if parts scratch easily.
ESD Tray Materials (Shipping & Reusable Trays)
- Anti-Static PVC (thin gauge)
For shipping applications and not for long term use. Coating will become less effective with time and use. Surface Resistivity see data page BVDC-H1X. This is generally a thin gauge option in .030 starting thickness. Surface Resistivity of material 10e^9.
- Conductive Styrene Black (thin gauge)
Stryene is Description: The material can be used for semi-reusable and reusable trays as ESD properties are set in the material. It is not a coated material. Surface resistivity 10e^4 to 10e^7. Black Conductive Styrene is generally a thin gauge option stocked in .030” starting thickness.
- PETG Anti-Static Material (thin gauge)
Description: For shipping applications and not for long term use. Coating will become less effective with time and use. Surface Resistivity see data page SC-E773. This is generally a thin gauge option in .030 starting thickness. Surface Resistivity of material 10e^9.
- ESD Material (heavy gauge for reusable material handling trays)
- HDPE Blue Ant-Static Material (heavy gauge)
Anti-static, generally blue, do not hold a charge for very long. A charge of 5000 volts is fully decayed in less than 2 seconds. This material requires a relative humidity of 15% or greater, so it won’t do the job in very dry atmospheres. The advantage of this material is that it does not slough conductive particles and is therefore usable in clean room situations. Trays meet minimum specifications per MILB-81705B. The base material, high density polyethylene, has high impact strength. Tested to less than 1012 ohms per square inch.
- HDPE Black Conductive (heavy gauge)
Conductive containers are always black because the material contains carbon black. The carbon black allows the containers to conduct, and therefore if grounded, they will not create an ESD moment. The conductivity of the containers is a permanent part of the high density polyethylene material used to manufacture the containers.There is, however, a tendency for minute particles of the carbon black to slough. This trait may make the containers unacceptable in certain clean rooms. Surface tested to make sure that it is 105 or less ohms per square inch.
- Conductive ABS (heavy gauge)
Used for long term ESD applications. Storage trays, etc. Expensive compared to conductive HIPS(above) and compared to standard ABS. See R63 Data Page.
- Inherently Static Disipative PETG
Used for long term ESD Trays. Storage and Handling trays. Expensive compared to conductive HIPS(above) or compared to standard PETG. This material has a blueish tint.
Cavity Options For Custom Trays
Custom Tray Cavities formed to exactly match part or made to contact part only in certain areas building in clearance(areas of no contact) Clearance can be for fragile components or for areas requiring optical clarity.
Custom Geometric Cavities can be formed in more standard geometric shapes to hold to part or act as a universal cavity tray for use with multiple part sizes. Simpler cavities in standard geometric shapes generally have lower tooling cost.
Prototype cavities (mini trays) can be made inexpensively or as a step in the design process. A small 3- 5 cavity tray can be made to insure tray function before the final tool is built. This step usually costs less then $ 250 and validates the cavity. Full size prototypes can also be made for low cost allowing for design and fit issues to be used prior to tray production
Advantages of Custom Trays
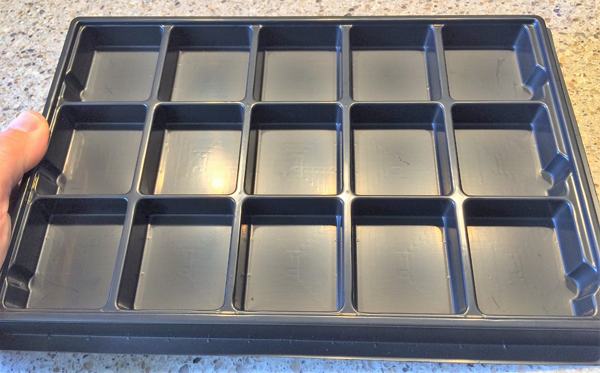
➔ Low Tooling Cost: Starting at $600 for basic designs in low volume applications.
➔ Labor Savings: Eliminating bags or special packaging materials can streamline the packaging process saving significant time while properly protecting parts.
➔ Economical Packaging Cost: Low part cost and cost per component. Trays are also low in weight reducing shipping costs.
➔ Part Counts & Inspection: Trays can be made to a specific even number like 50 or 100 cavities per tray facilitating counting. Cavities can be numbered if needed for inspection.
➔ Cleaner Than Corrugated: No corrugated dust with plastic trays. The plastic can be used in clean-rooms or for medical applications depending on material choice. See material information below.
➔ Reusable Packaging: Trays can be made for internal plant handling and for shipping applications. Re-usability reduces packaging cost per component vs. disposable custom trays.
➔ Custom Tray Cavities: Formed to exactly match part or made to contact part only in certain areas building in clearance(areas of no contact) for fragile or areas requiring optical clarity. More information below.
➔ Material Options: Depending on part and application. For instance several ESD materials are available for electronic components. PETG is often used for optics and lenses sensitive to out-gasing (see material section below).
➔ Used With Automation: Able to be used in Automation Processes. See custom design features below.
➔ Overall Tray Size: Tray to fit current box configuration, or standard off the shelf boxes.
➔ Recyclable: Plastics used for trays are 100% recyclable, and trays are often reusable.
Applications For Custom Trays
- Shipping Trays
- Material Handling Trays
- ESD protection Trays
- Medical Trays
- Drip Trays
- Automation Trays
- Packaging Trays
- Automotive Style Dunnage Trays
- Food & Bakery Trays
- Retail Trays
Related Documents
RELATED DOCUMENTS
Click on the following link(s) for relevant document. Contact customer service for additional information, data pages, or msds sheets.
For HDPE Plastic Bins: Anti Static Material Guideline